10+years in packaging machinery industry.
+86 13751707210 (Tel/ Whatsapp) Email:info@nolijmachinery.com
How to Choose the Right Sachet Packing Machine Based on Product Type (Granules, Powder, Liquid, Paste)? Is Sample Testing Needed?
Selecting the optimal sachet packing machine is critical for efficiency, product integrity, and cost control in food, pharmaceutical, and chemical industries. The physical properties of your product – whether granules, powder, liquid, or paste – directly determine the ideal machine configuration. This guide explores key selection criteria and emphasizes the importance of sachet packing machine sample testing.
1. Granules (e.g., Rice, Sugar, Snacks)
- Machine Requirements: Granules require tailored dosing based on uniformity. For small, uniform granules (e.g., rice, sugar) with lower precision demands, volumetric cup fillers are cost-effective and efficient. For irregular, mixed, or fragile granules (e.g., potato chips, mixed nuts, cereal), multihead weighers are essential to achieve high accuracy (±0.5g) and minimize product damage.
- Key Features:
- Volumetric Cup Fillers: Adjustable cup sizes, vibration-assisted filling, simple maintenance.
- Multihead Weighers: 14-24 weigh buckets, intelligent combination algorithms, gentle product handling.
- Sample Testing Value: Critical to verify:
- Cup filler accuracy with uniform granules under vibration.
- Multihead weigher’s ability to handle irregular shapes without breakage.
- Packaging material puncture resistance (e.g., for sharp-edged granules).
Click here to see granule packing machine
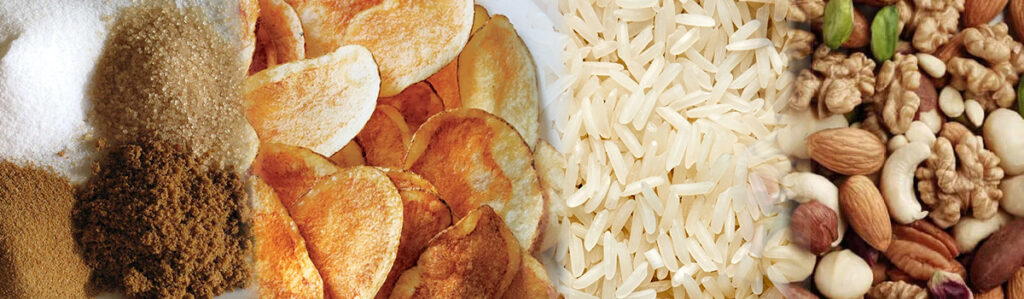
2. Powder (e.g., Spices, Protein Powder, Milk Powder):
- Machine Requirements: Powders are prone to dusting and bridging. A vertical sachet packing machine with a precision auger filler is standard. Augers with anti-bridging designs (e.g., conical hoppers, agitators) are crucial. Excellent dust extraction is mandatory.
- Key Features: Sealed auger systems, high-precision servo-driven augers (for expensive powders), advanced dust collection ports, easy-clean design (sanitary finishes). Powder-specific auger designs (ribbon, paddle).
- Sample Testing Value: Critical to assess dust control effectiveness, measure filling accuracy (especially with cohesive powders), test material compatibility to prevent static cling, and ensure complete sealing despite potential powder contamination on the seal area.
Click here to see powder packing machine
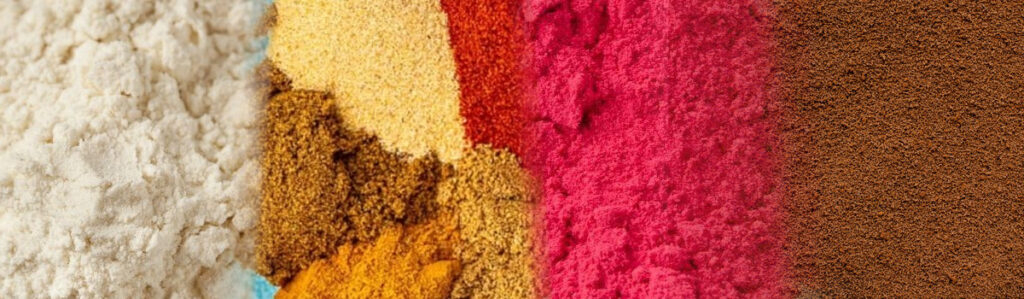
3. Liquids (e.g., Sauces, Oils, Vinegar):
- Machine Requirements: Liquids demand leak-proof solutions. Liquid sachet packing machines use piston fillers or peristaltic pumps. Piston fillers handle thicker/viscous liquids well; peristaltic pumps excel with thin liquids and offer high hygiene. Machines require drip trays, nozzle wipers, and often bottom sealing for stability.
- Key Features: Corrosion-resistant materials (316L SS), CIP/SIP capabilities, precision pumps, nozzle anti-drip systems, robust longitudinal and transverse sealing. Bottom gusset options for stand-up pouches.
- Sample Testing Value: Vital to test sealing integrity under pressure/squeeze, verify fill volume accuracy (especially with foaming liquids), assess nozzle retraction to prevent dripping, and ensure packaging material barrier properties (e.g., against oxygen, moisture).
Click here to see liquid/sauce packing machine
4. Pastes & Semi-Solids (e.g., Toothpaste, Mayonnaise, Cosmetic Creams):
- Machine Requirements: High viscosity requires force. Piston fillers are the primary choice for paste sachet packing machines. Positive displacement pistons ensure accurate dosing. Machines need wider sealing jaws to handle potential material contamination and strong drive systems for thick products. Augers might handle some softer pastes.
- Key Features: Powerful piston drives, large-diameter product inlets, heated hoppers/pistons (for temperature-sensitive pastes), easy disassembly for cleaning, specialized nozzles for high-viscosity flow. Often requires slower operating speeds.
- Sample Testing Value: Imperative to confirm filling consistency (no air pockets), test sealing strength despite potential paste seepage, evaluate product recovery from the system (minimize waste), and check for smooth flow without clogging.
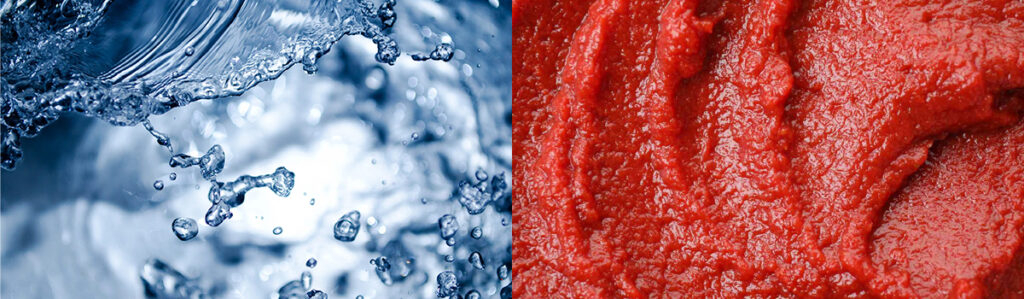
Why Sample Testing is NON-NEGOTIABLE Before Buying a Sachet Packing Machine:
Relying solely on specifications is risky. Sample testing using your actual product and intended packaging material on the shortlisted sachet packing machine is essential because:
- Validates Compatibility: Proves the machine can reliably handle your product’s specific flow characteristics, density variations, and potential quirks (dust, foam, stickiness).
- Confirms Accuracy: Demonstrates achievable fill weight/volume precision under real conditions.
- Tests Seal Integrity: Ensures the heat, pressure, and timing settings create strong, hermetic seals resistant to product interference and leakage.
- Assesses Speed & Efficiency: Reveals the actual sustainable production rate without jams or quality compromises.
- Optimizes Settings: Allows engineers to fine-tune parameters (fill time, auger speed, piston stroke, sealing temp/pressure) for optimal performance.
- Packaging Material Verification: Tests how well the chosen film/laminates run on the machine and protect the product.
- Identifies Potential Issues: Uncovers unforeseen problems like product degradation, excessive waste, or maintenance challenges early.
- Builds Confidence: Provides tangible proof of the sachet packing machine’s suitability before final investment.
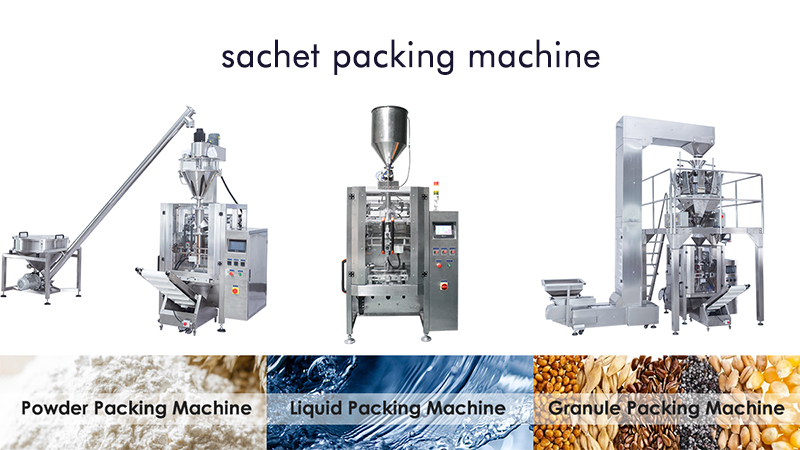
Conclusion:
Choosing the right sachet packing machine hinges critically on understanding your product’s physical properties. Granules need gentle flow control, powders demand precision and dust management, liquids require leak-proof systems, and pastes need powerful, positive displacement. While machine types (vertical form-fill-seal being most common) and filler technologies (auger, piston, cup, pump) provide a framework, there is no substitute for rigorous sample testing. Partnering with a sachet packing machine manufacturer who offers comprehensive testing using your real product and packaging is the single most reliable way to ensure seamless integration, product quality, and long-term production success. Never skip the sample trial phase.